A Plan for Every Asset
Building a plan… Especially, for when the plan breaks…
Fleet management isn’t just about maintaining machinery; it’s about optimizing assets for maximum efficiency, reliability, and profitability. By aligning with well-established principles and practices, organizations can unlock the potential for enhanced operational performance. This post will delve into essential strategies for establishing a robust asset management plan and how they contribute to achieving excellence in fleet management.
Building the Plan for Every Asset Serial Number
Step 1: Asset Inventory and Data Collection
Begin with an exhaustive inventory of all assets, documenting their serial numbers, specifications, and current condition. This includes identifying critical assets and hot list to inspect and be aware of as you go into battle of day to day combat with your fleet. Accurate data, and physically touching the machines are foundational for effective management. This includes but is not limited to a smart asset id number that tells you and the operator something about the machine, class, and critical items like weight, width and height. This can also be supplemented with a QR Code that links to the asset details sheet.
Step 2: Lifecycle Analysis
Utilize Vorster’s lifecycle costing method to analyze each asset’s total cost of ownership. This should include acquisition costs, operational expenses, and potential salvage value. Click below to request a demo and access to the latest version that can help you build your Capex Budget and Hotlist of critical path machines. The total cost of ownership should include owning, and operating costs as well as expected utilization rates, average age of similar assets in your fleet and the overall reliability expectations of this asset class. These are the key factors that should be used product your rate and overall budget.
Step 3: Risk Assessment
Conduct a thorough risk assessment for each piece of equipment. Identifying risks enables proactive measures, reducing downtime and enhancing safety. Focus on assets that work as a system first and the prioritize by critical jobs and asset value. Think about how you can incorporate these concepts into the asset id number too.
Step 4: Establish Performance Metrics
Define KPIs relevant to each asset. These could include utilization rates, maintenance uptime, and repair types. Tracking these metrics helps ensure accountability and drives performance. This ensures that you and your team understand what winning looks like and how to impact the overall performance of your fleet.
Step 5: Strategic Planning
Incorporate the CEMP WAY's strategic asset planning by aligning fleet needs with organizational objectives. Consider future projects and how equipment can be optimized to meet upcoming demands.
Step 6: Data-Driven Maintenance
Invest in technology and software that enables you to build a quality maintenance plan and automate the process in the heat of battle. This reduces unplanned downtime, unplanned repairs, and ensures assets are serviced based on actual needs rather than arbitrary schedules.
Step 7: Periodic Review and Continuous Improvement
Set regular review intervals to assess performance against benchmarks. Utilize deviations from expected performance as learning opportunities to refine strategies and improve operational outcomes.
Conclusion
Implementing a world-class fleet management plan based on the teachings of Mike Vorster, The CEMP WAY, and Caterpillar’s equipment economics is a formidable but rewarding task. Organizations that invest in these methodologies not only enhance their operational efficiency but also set a standard in the industry that few can match. By focusing on each asset’s serial number and utilizing a systematic approach, companies can achieve sustainable growth and maintain a competitive edge in the ever-evolving landscape of equipment management. Embrace this journey, and transform your fleet management practices into a model of excellence.
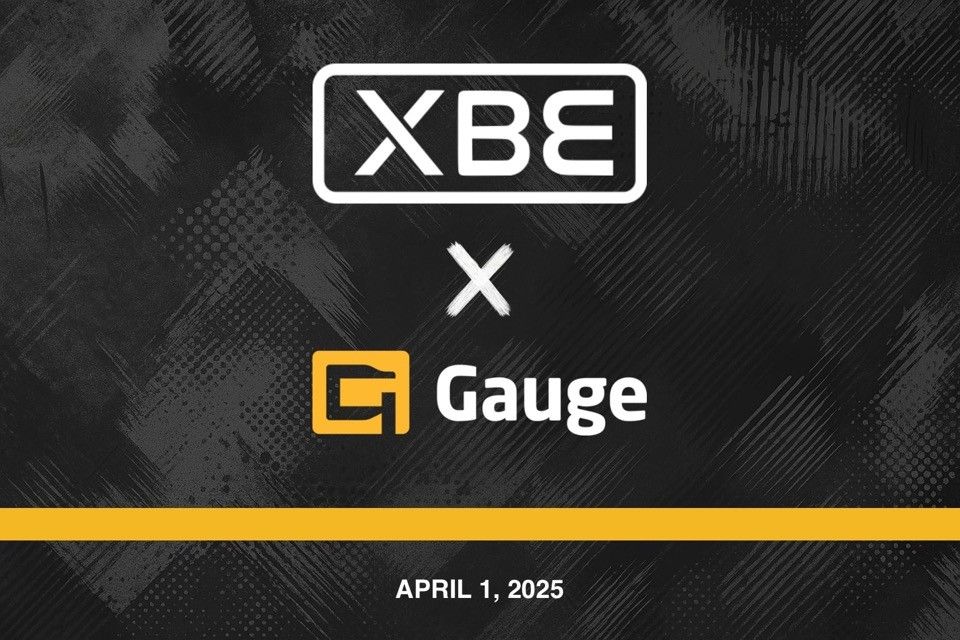
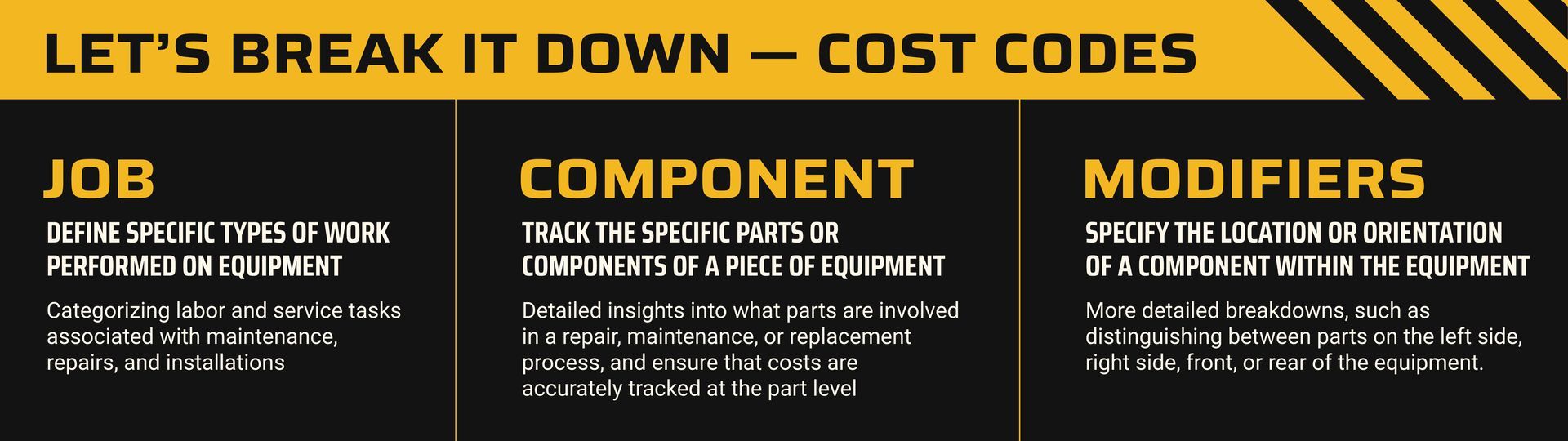
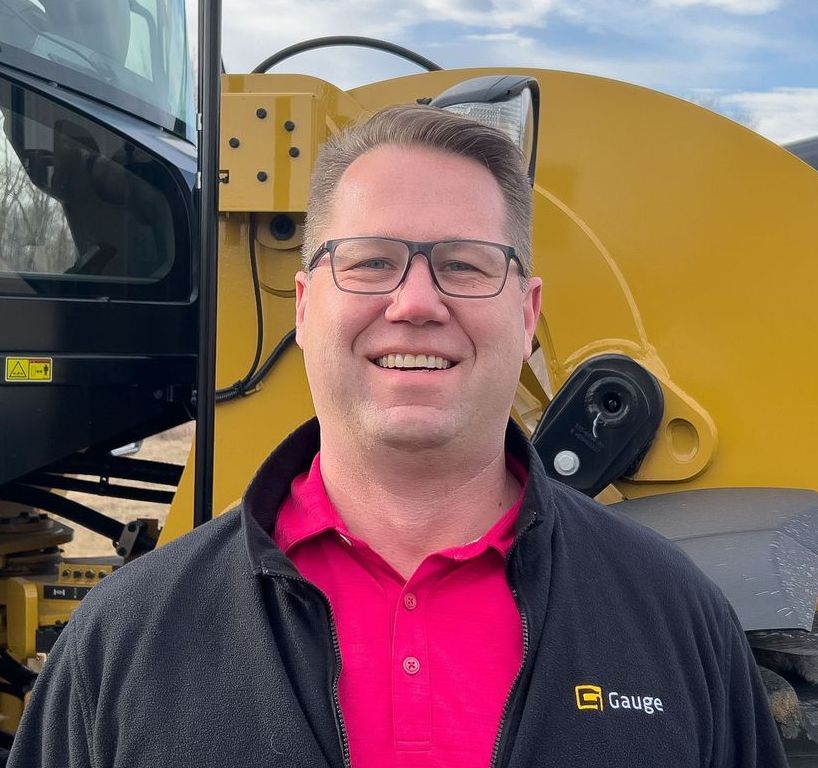