WHO CAN DO IT ALL???
Do You Know Anyone Who Can Do It All? Dirty vs Clean fingernails...
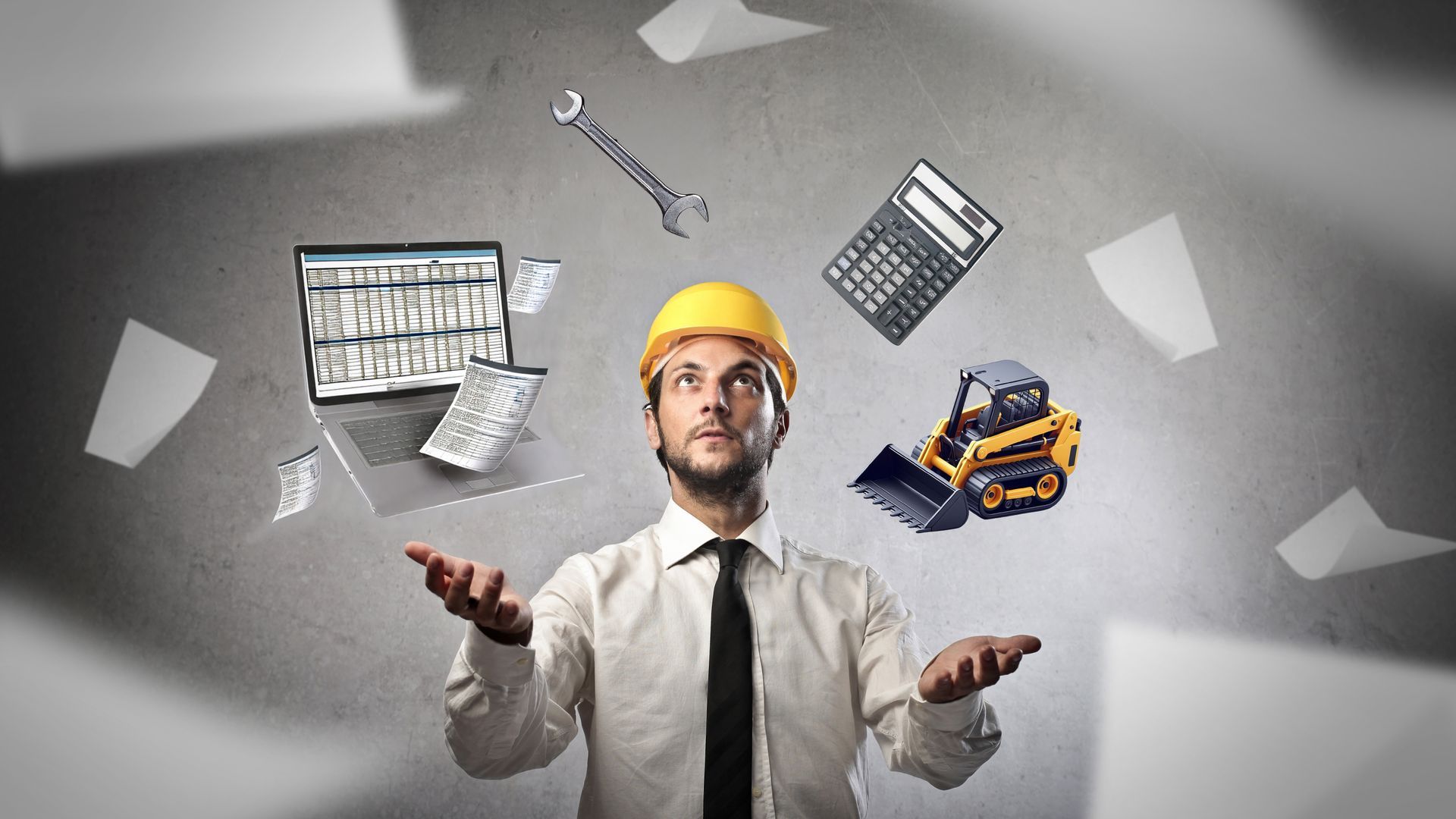
? Do you know anyone with an accounting degree and a knack for fixing heavy machinery?
? What about someone with a CDL who also loves coding PowerBI to analyze data?
? Ever met someone who enjoys both spreadsheets and working on equipment in the field?
If you're drawing a blank, you're not alone. These combinations are rare—and yet, organizations often expect equipment managers to master both worlds: financial planning and hands-on equipment management.
The Two Sides of Equipment Management
Mike Vorster, a thought leader in equipment management, identifies two distinct types of job responsibilities that equipment managers must juggle:
- Financial Responsibilities
- Preparing CAPEX budgets
- Managing expenses
- Analyzing asset costs, utilization, and replacement schedules
- Operational Responsibilities
- Scheduling and ensuring timely maintenance and repairs
- Negotiating with production teams for access to equipment
- Supervising inspections, fueling, greasing, and other daily maintenance tasks
On paper, these roles seem complementary. In practice, they require vastly different skills, personalities, and areas of expertise. Financial tasks demand analytical thinking and attention to detail, while operational tasks call for hands-on problem-solving and technical know-how.
Bridging the Gap
Too often, organizations expect a single person to seamlessly manage both sides of the equation. While some individuals may excel at wearing multiple hats, it’s unrealistic—and often counterproductive—to rely on one person for everything. Maintenance and repairs can’t be delayed indefinitely, just as financial oversight can’t be ignored. Neglecting either side can quickly lead to inefficiencies, increased costs, and downtime.
Vorster’s perspective challenges us to rethink the structure of the equipment management function. How do we ensure that both financial and operational needs are met without overburdening one person?
Structuring the Asset Management Team
Let’s consider the six core responsibilities of equipment managers or asset managers. These include:
- Financial Management
- Operational Oversight
- Maintenance Planning
- Safety and Compliance
- Equipment Strategy and Utilization
- Vendor and Stakeholder Coordination
Instead of centralizing these tasks under one role, organizations can explore structuring the asset group to play to individual strengths:
Split Roles: Separate financial and operational responsibilities into distinct roles, allowing specialists to focus on their expertise.
Collaborative Teams: Build teams where financial analysts, maintenance planners, and field managers work together.
Technology Leverage: Use tools like Gauge Telematics to simplify data sharing, tracking, and reporting, bridging the gap between financial and operational insights.
Moving Forward
At its core, equipment management is about balance—balancing costs with uptime, planning with action, and financial stewardship with operational realities. But that balance doesn’t have to rest on one person’s shoulders. By redefining roles and investing in the right processes and tools, organizations can empower their teams to meet the demands of both sides.
How does your organization structure its asset management team? Are your equipment managers set up for success, or are they expected to “do it all”? Let’s start a conversation about building better processes that make room for technology—and people—to shine.
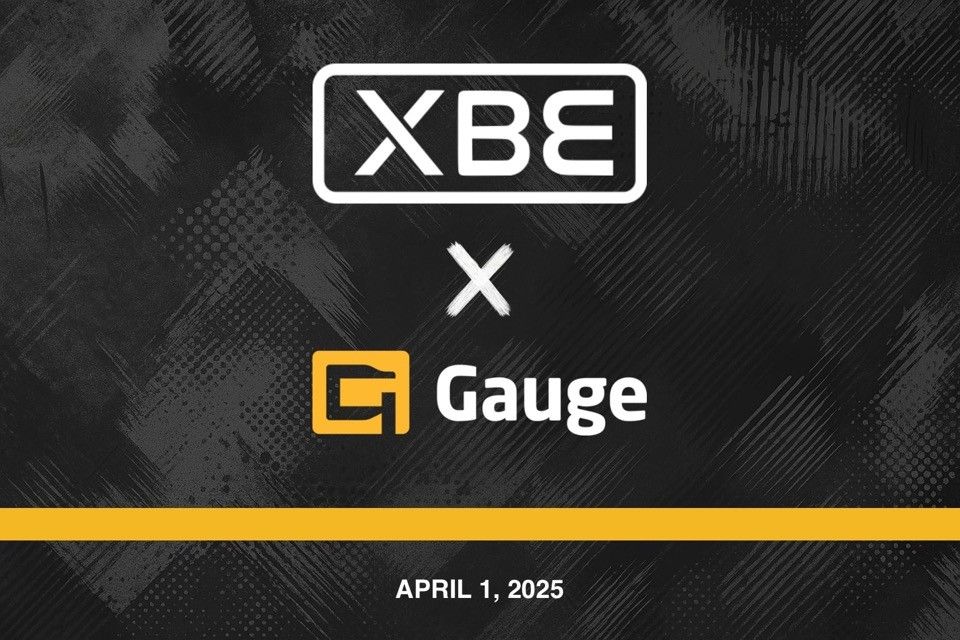
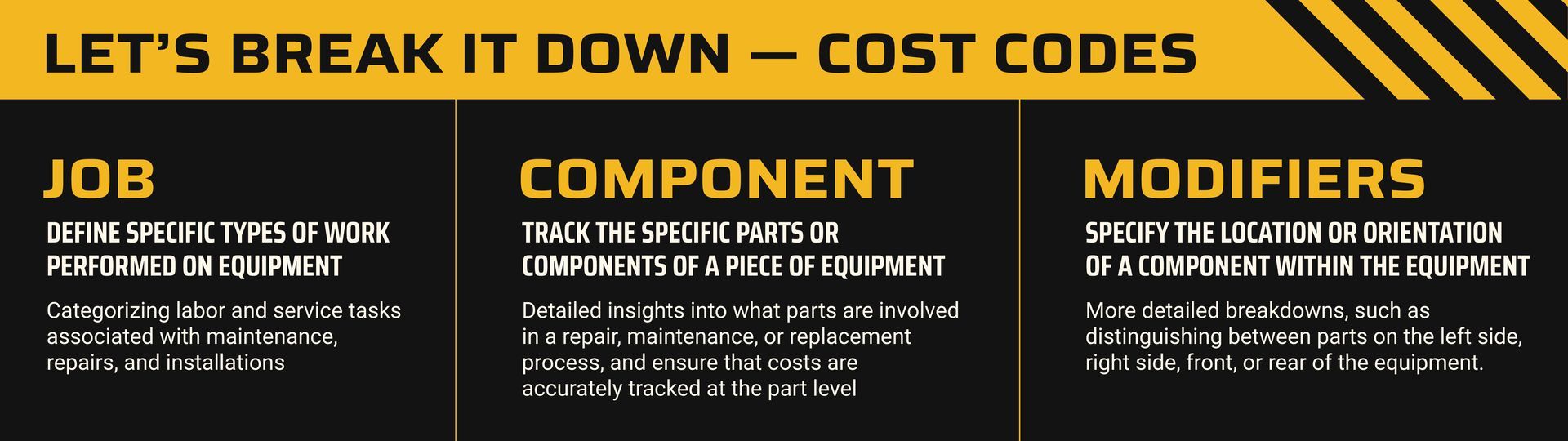
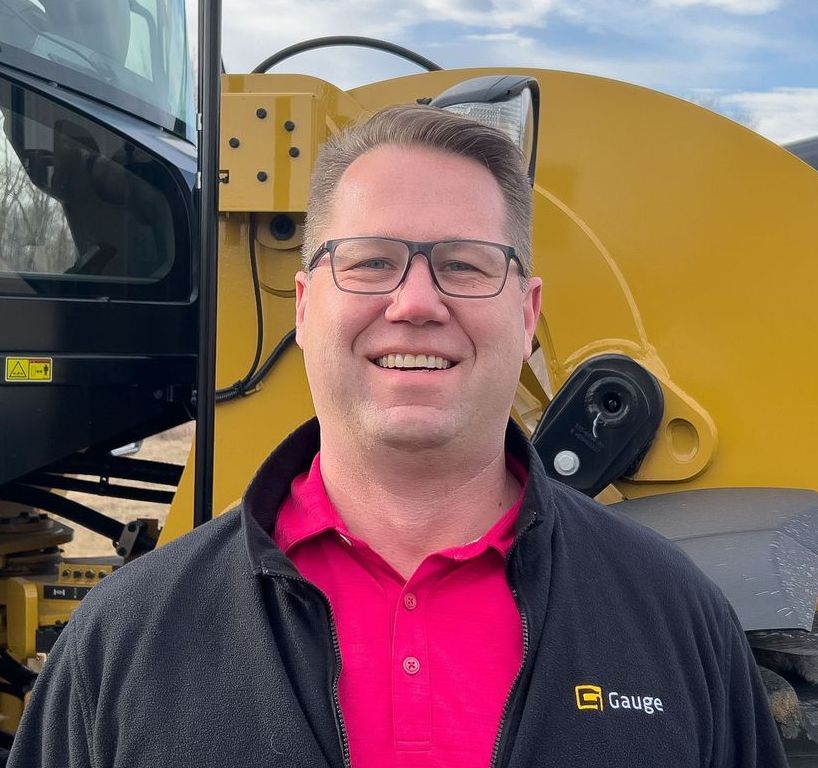